GCR accelerates investment with new recycling plant to support circular economy
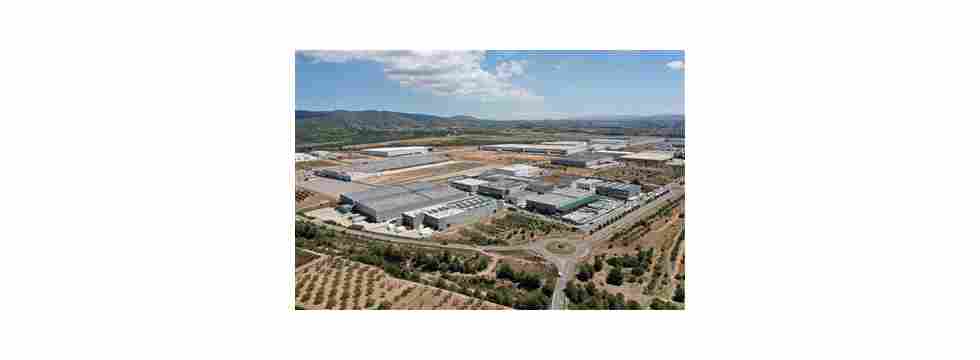
GCR Group has announced the plan to open a new dedicated recycling plant in Castellet i La Gornal, Barcelona, Spain, enhancing the group’s capability to serve increased global demand for its CICLIC range of recycled polyolefins (R-polyolefins). The 200,000 Tonnes (200kT) plant, commissioning in 2023, when fully operational in 2025, will be one of the largest of its kind and is a significant step for the group; the capacity for CICLIC combined with that for the GRANIC® range of sustainable mineral-filled masterbatches and compounds will reach 500kT. GCR has a global reach, exporting 85% of its sales to over 100 countries.
GCR strongly believes collaboration on the developing of new products and applications is essential to accelerate the circular economy. The company hosts the ‘co-creation’ process across the value chain, where brand owners, converters, and suppliers can come together to practically test ideas and create precisely-defined sustainable solutions.
Whilst many announcements support the circular economy, this investment will enable GCR to host a leading position in Europe and reflects a long-term vision created more than 20 years ago when GCR Group was founded and a track record of continuous investment in that vision. This long experience in materials technology, innovation, and a relentless focus on quality and consistency enables GCR to partner with companies to deliver practical and realistic answers to sustainability questions. “Our essence, driving force, and operational excellence are focused on ‘Innovating our Sustainable Tomorrow’, “ says Managing Director Joan Prats. “Our success is based on the experience of our people and investment in state-of-the-art equipment, but also coupled with agility and a collaborative approach”, he adds.
When brand owners think about using recycled plastics, they are often concerned about issues such as consistency of supply, traceability and whether the mechanical performance can match the virgin polymers they currently use. For many development engineers, reaching future internal and external sustainability targets is increasingly challenging. However, GCR’s existing CICLIC up-cycled products and ‘co-creation’ approach to customisation can solve these problems.
The CICLIC -polyolefins are based on up-cycling fully traceable waste streams and can deliver similar and consistent material properties as the virgin plastic. By replacing virgin plastic with these grades, Carbon Footprint certification can be 60-80% lower without compromising performance and quality. GCR believes companies facing sustainability challenges can find the answers through GCR’s products and long experience.
GCR’s extensive experience in polymer materials technology helps develop customised solutions in partnership with suppliers and end customers in a collaborative partnership. The new production plant is complemented by a recently opened Innovation Hub with ‘Co-creation’ space, enabling the development of new formulations and the production and testing of compounds on a pilot plant.
The new plant investment provides sufficient capacity to address high-volume demands in applications such as rigid and flexible packaging, automotive, construction and home and garden markets. In addition, GCR carries out toll manufacturing for food contact applications using advanced recycling technology, enabling impurity-free materials and certified to EuCertPlast.
GCR strives to accelerate the deployment of circular economy models. “We dare to dream; we are determined to set new standards, offering high-performance materials that contribute to environmental stewardship,” says Prats.
The company will be showcasing its capabilities at the K-Messe, Hall 8 Stand K27. In particular, GCR has created specifications for the exact solution that can replace 100% of virgin plastics through collaboration and innovation across the value chain.