SABIC and Japan Steel Works collaborate on SABIC’s TF-BOPE resin for flexible packaging
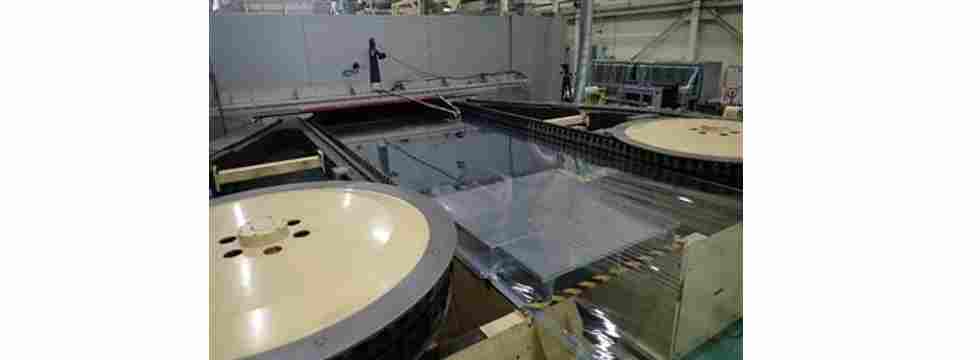
Processability of SABIC® LLDPE BX202 resin validated in extensive trials on biax film pilot line at JSW’ Technology Center in Japan
SABIC’s TF-BOPE resin supports down-gauging and corresponding reductions of up to 50 percent, offering a mono-PE film solution designed for end-of-life recycling in existing recycling streams for flexible packaging
SABIC, a global leader in the chemical industry has announced that The Japan Steel Works, Ltd. (JSW) has validated the use of SABIC® LLDPE BX202, a linear low-density polyethylene resin specially developed for processing on tenter frame extrusion equipment for biaxially oriented PE (TF-BOPE) packaging film. The value chain collaboration endorses the use of SABIC’s TF-BOPE material on JSW film lines, extends the machine supplier’s footprint into the BOPE film market for flexible packaging, and underscores SABIC’s role as a forerunner in this market segment.
Sami Al-Osaimi, Executive Vice President Petrochemicals at SABIC commented, “There is a growing market trend and demand for mono-material solutions to facilitate the end-of-life recycling of used packaging products while at the same time supporting the efforts of brand owners and packaging manufacturers to down-gauge their applications and meet ambitious reduction targets. The partnership with JSW has confirmed our strong commitment to accelerate the implementation of advanced material and equipment solutions for flexible packaging by working with global value chain partners who share our mindset to reduce, reuse and recycle as we contribute to a circular plastics economy.”
Extensive trials with SABIC LLDPE BX202 resin on a pilot film manufacturing line at JSW’s Extrusion Technology Center in Hiroshima have demonstrated the excellent performance of the material. As a result, this TF-BOPE grade is currently considered the best-in-class to run on existing tenter frame film lines for BOPE as well as on slightly modified equipment for biaxially oriented polypropylene (BOPP). Toshiyuki Ninomiya, Vice Plant Manager, Hiroshima Plant for JSW explained, “After testing SABIC’s LLDPE BX202 material in our Bi-Axial Film Stretching pilot line, we were positively surprised by the performance of it. Its excellent processability combined with good mechanical properties makes this material a great addition to our recommendable materials portfolio for our customers and strengthen our position in the BOPE market. By collaborating with SABIC for use of their overall high-performance TF-BOPE resin on our advanced film extrusion lines, we are actively promoting the broader implementation of more efficient and sustainable, circular ‘mono-materialized’ film solutions designed for recycling.”
SABIC’s LLDPE BX202 material combines outstanding processability with good mechanical and optical properties, including clear transparency and twice the impact strength, puncture resistance, tensile strength and stiffness compared to conventional blown PE film of equal thickness. This means that SABIC’s material offers significant potential for further down-gauging and corresponding reductions in weight, material consumption and carbon emissions. At potential packaging material reductions of up to 50 percent vs. incumbent blown PE film, this also translates into potentially higher line speeds with shorter cooling times, maximizing the productivity of applications.
Furthermore, the mono-PE material enhances the recyclability of final flexible packaging applications at the end of their lifespan without compromising the integrity of the packaged products such as frozen food, fruit and vegetable packaging applications. SABIC’s TF-BOPE polymer is also available in certified circular as well as certified renewable grades from TRUCIRCLE™ portfolio.